CeraCode® Flex: Individual component fingerprint
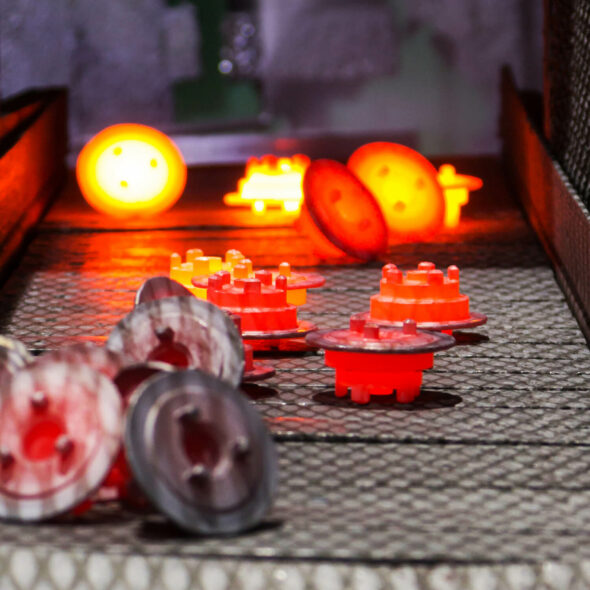
Products are often exposed to extreme process temperatures or highly deforming process steps during their creation, processing or finishing, which completely or partially remove the original shape of the component. With the help of CeraCode® Flex, we make it possible to clearly identify such components, even if markings have been severely deformed or partially destroyed.
Description
CeraCode® Flex covers both the marking and identification of components. The marking is carried out with a specially developed ink that can also be used to mark hot surfaces (up to 350 °C). The marking does not have to conform to any standard and can be applied in various ways, such as transfer printing or shot marking.
For identification, the marking is photographed, the relevant parts are filtered out and a digital fingerprint is created using DescriptorID technology. These IDs can be stored in a connected database, allowing product and process data to be clearly assigned to the components. If only parts of the original marking remain after further production steps, this technology is used to deduce the original coding and therefore the component number. This ensures that the parts can be traced.
In addition, DescriptorID technology can be used as a further security feature for standard codes (e.g. DMC), as it can also differentiate between multiple printed markings with the same code content and thus recognise counterfeits or improve recognisability.
Advantages
- Independent of standardized code formats
- Robust against partial destruction of the marking
- Easier to apply than needles or lasers
- Can be applied to hot surfaces (up to 350 °C)
- Identification even at high degrees of deformation and temperatures above 1.300°C
- Traceability and data exchange throughout the entire process chain
- Additional security feature and unique component identification
Specifications
Labelling can be applied automatically, semi-automatically or manually. In addition to pure labelling, the intelligent camera modules can also be installed individually along the process chain. Our complete solution includes the design, integration and networking of the systems.
Labelling can be carried out using either shot marking or transfer printing. With shot marking, the components are labelled with a special paste. With transfer printing, the codes are applied using a stamp and a highly viscous ink.
Component identification is carried out using an integrated camera system to generate IDs. These are stored in a linked database, synchronised and referenced if necessary. Customised indexing ensures fast access.
The IDs can be buffered in the camera memory and stored in a connected database. The system can be connected to existing MES/ERP systems via the APIs we provide and process and product data can be clearly assigned. Separate modules can also be used to exchange data securely and confidently across company boundaries.
In cooperation with
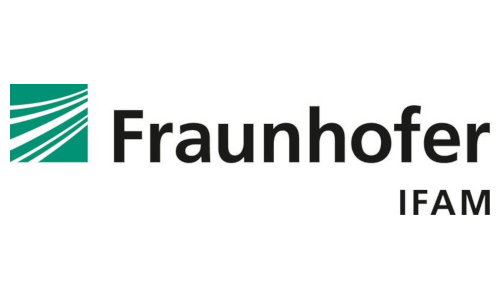
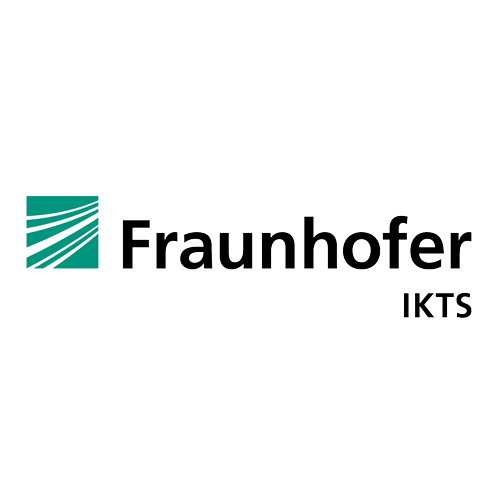