Process optimization in press hardening
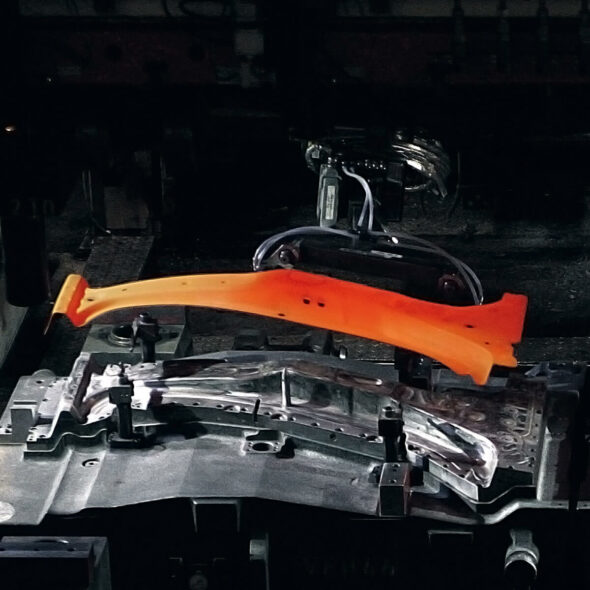
Challenge
Due to the combination of high strength, low weight and precise shaping, press-hardened components are increasingly used in the automotive industry. The increasing production numbers require component-specific identification. Only this makes it possible to analyse the causes of problems in production, to precisely limit faulty batches, to carry out a full CO2 balance and to pass on production data to partners.
Consequences of a lack of labelling are:
- Increased risk of errors and rejects due to lack of component traceability
- Difficulty in analysing the causes of problems in production due to lack of transparency in the process chain
- Poorer rating in sustainability criteria due to lack of recording of CO2 footprint
In cooperation with press hardening experts, a variety of starting points were identified in order to create tangible added value with the digitalisable solutions from Senodis and to increase the efficiency of the customers.
Use case: Production start-up (testing of start-up parts)
CeraCode® marking on each component Production still possible during QA of first parts Scanning of the respective parts and precise localisation Part-specific release possible
Often, the parts that are the first to leave the oven after a downtime are sorted out. The reason: there is a lack of valid data for quality assurance. With our holistic solution CeraCode® , the necessary information is collected so that less or no rejects are produced right from the start.
- Unrestricted, continuous production even during start-up parts testing
- Prevention of component mixing
- Possibility of opening up new production capacities
Use case: Internal quality complaint
CeraCode® marking on each component Detection of quality deviations Scanning of the respective parts and precise localisation Part-specific release possible
An elementary pillar of quality assurance is testing during series production. If specification deviations occur that call the component quality into question, it must be possible to precisely delimit defects. Mixing with good parts must also be avoided. Our modern track and trace solutions support you in this.
- Faster and more accurate fault location
- Reduction of components to be scrapped
- Shorter sorting measures